- September 07, 2023
- By Karen Shih ’09
When record-shattering quarterback Taulia Tagovailoa and the rest of the Terps football team take the field this weekend against Charlotte, every custom-fit cleat, high-tech helmet and broken-in game ball will be perfectly prepped, thanks to Senior Director of Football Equipment Operations Drew Hampton and his staff.
They order, inventory and distribute everything from blocking sleds to tackling dummies; shoulder pads to shower sandals—anything that the more than 200 football players and staff could possibly need throughout training camp and the regular season.
“I know we’re not out there playing. We’re not out there coaching. But we’re so invested, and we play an important role behind the scenes,” said Hampton, who oversees two full-time staff members, Jason Smith and Nathaniel Park ’90, as well as 15 student managers.
Hampton likes to say that he grew up going to “training camp, not summer camp.” His father, Bill, ran the equipment operation for the New York Jets for nearly four decades, and Drew Hampton and his four brothers have all carried on the tradition. He’s worked for the Jacksonville Jaguars, the Washington Commanders and Western Kentucky University, and came to the University of Maryland in 2016. He always looked up to fellow Long Islander Boomer Esiason ’84, and was thrilled to join the Terps.
Hampton shares how he mixes old-school tactics and the latest tech to get the best gear for the Terps, why shaving cream and mud are essential for every football he prepares, and the toughest stains to get out—as well as the fate of Head Coach Mike Locksley’s outfit after he was doused in mayonnaise when the Terps won the Duke’s Mayo Bowl last year.
On putting together uniforms:
The main component of our job as equipment managers is to stay abreast of all the newest technology and protective equipment. We pay attention to the testing going out there. It’s not cookie cutter, because every player that comes through the door is a different size and shape and plays a different position.
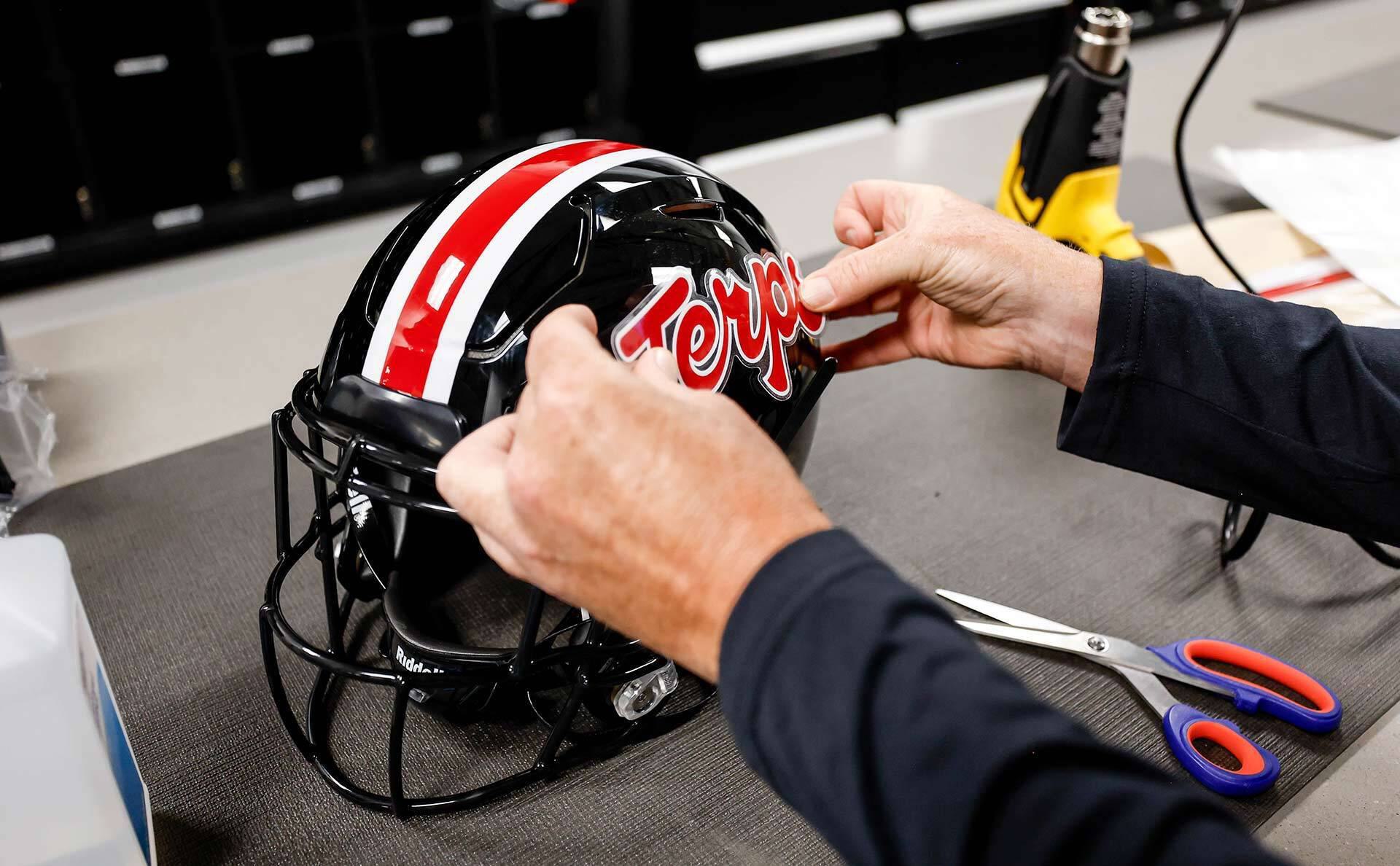
For helmets, we do 3D custom scans of our players’ heads. I’ll put a neoprene bonnet on them—almost like a scuba hood—and then we get all the data points for their head specifically. We upload it to the manufacturer Riddell’s server, and they build it, custom-fit to his head. It’s pretty awesome.
Every player has a practice helmet and a game helmet, and they should last the duration of his playing career here. At the end of each season, we send them back to the manufacturer for reconditioning and recertification. They’ll get a fresh paint job and make sure all the interior components are functioning the way they should. Then we rebuild it here with decals, face mask, jaw pads, chin straps.
For the shoulder pads, we go old school. We have this tailor’s tape, and we measure across the back and across the chest, almost like you’re fitting a suit. Players ask for the smallest pads, as minimalist as possible, but we walk that line to find the balance between comfort and safety. It’s like a sworn oath: We put the players’ health and safety before anything else.
Each set of pads should carry a player through spring training, summer training camp and the season, and then we reevaluate. What happens is, a freshman comes in here, 18 years old, 200 pounds. But then between working out with our strength and conditioning coaches and eating what our team nutritionist feeds them and maturing, they keep growing. So they’re not locked into a size until their junior year.
For cleats, we use this Under Armour prescription chart based on your position, weight, height and shoe size. Most players have three or four pairs of cleats in their locker as well as two pairs of training shoes for the weight room, and I encourage the guys to change out the cleats as often as possible. The structural integrity just breaks down and makes you susceptible to a foot or ankle injury, so every two or three weeks they’ll get new ones.
We have this great relationship with Under Armour. Since founder Kevin Plank ’96 is a grad, they do cool things like test products here, and based on our feedback, they may develop it or make changes. They usually come through three or four times a year with new products.
On game days:
For home games, players do a walkthrough Friday morning, then we go through and clean the locker room so it’s what coach calls “recruit ready.” Perfect and pristine. Then we’ll go down to the field area and place our equipment trunks that we need for game day, which have everything from spare helmets to chewing gum—anything they could ask for. We also have the sideline communication systems, which allow our 10 coaches upstairs and 15 on the field to communicate with each other.
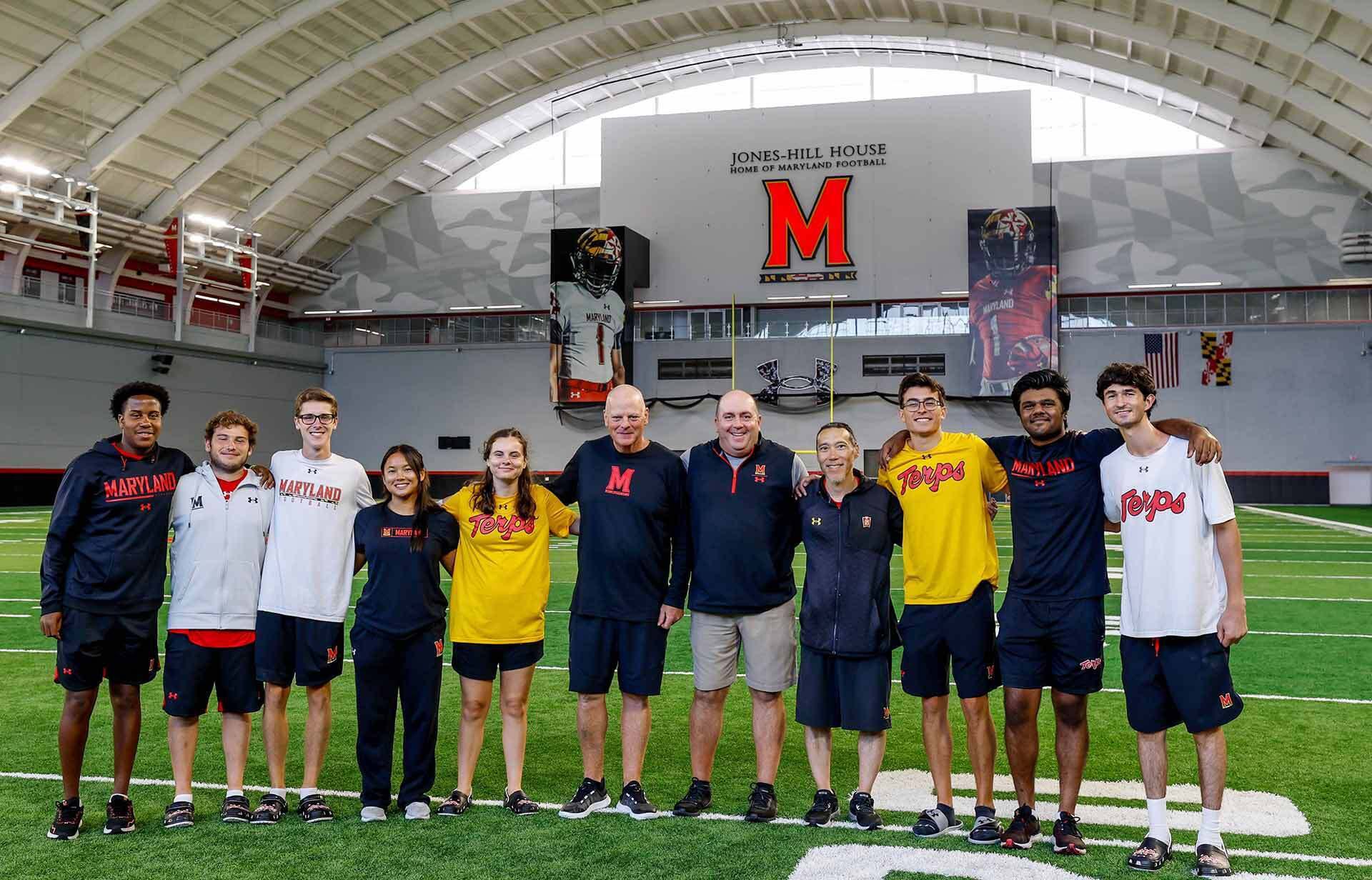
We prep 24 footballs for the game, even though we only turn in 12 to the officials. Footballs have evolved so much from the ’80s and ’90s. Then, it was almost like you just took them out of the box, inflated them to 13 pounds of pressure and put them on the field. Now, it takes an hour to prepare each ball: wiping it down with shaving cream, using linseed oil, treating it with Lena Blackburne mud. It makes it feel broken in, and it’s much easier for a quarterback to throw. We use a couple hundred balls per season.
For away games, we have our own tractor trailer, and we travel with anywhere from 12- to 15,000 pounds worth of equipment. We start loading the trailer on Tuesday for Saturday games. It takes us about two days, playing Tetris with all the equipment boxes that hold apparel, training supplies, sports medicine to load it up. Then Thursday after practice, I’ll get on the bus with about eight student managers and we’ll ride up there, arriving in the middle of the night.
The next morning, I’ll rally everyone to unpack at the stadium. Our goal is to be unpacked before the team sets out, so in case we forgot anything, they can bring it. Knock on wood, it hasn’t happened yet!
During games, I stand next to Coach Locksley most of the time so we can react quickly if there are any equipment breakdowns: a guy’s face mask comes loose, a jersey tears, or something as simple as a shoe lace breaks. If it’s a pivotal point in the game, every second counts, in terms of getting him back on the field.
Then after the game, it’s all hands on deck, and we are usually completely packed up—while the players and coaches get showered—and out of the stadium in an hour.
On laundry:
When they were building Jones-Hill House, our facilities director told me to shoot for the moon, so I requested six washers and six dryers—and I got it! We used to only have two of each, which took four hours a day. Now, the washers can do up to 250 pounds, so it takes half the time.
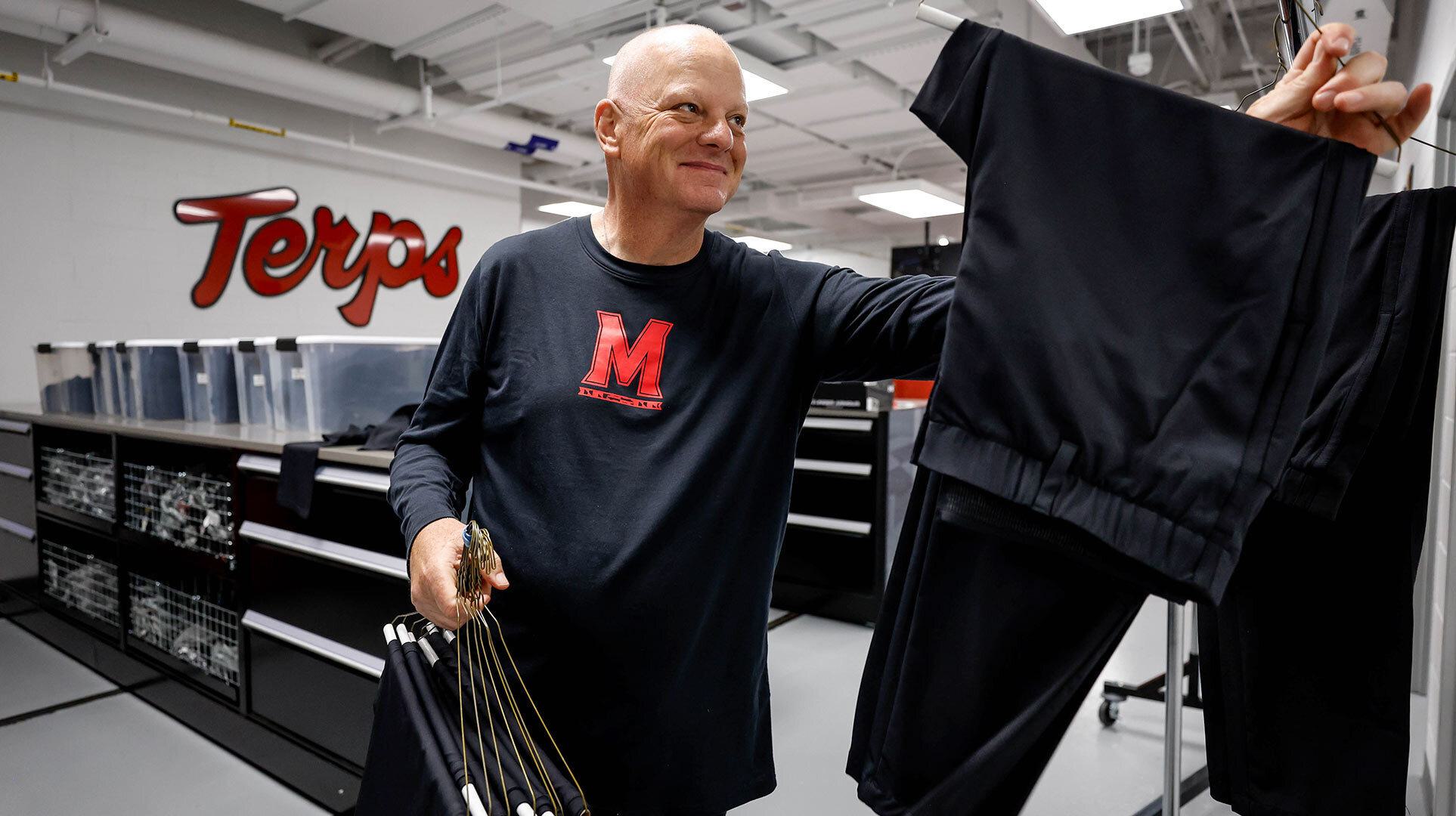
Rye grass and Gatorade are the hardest things to clean. A lot of football fields use Bermuda grass, but when the frost hits, they’ll overseed with rye because it grows better in cooler weather. For some reason, those stains are just really, really hard to get out. And for Gatorade, the red is the absolute worst.
The great thing is I have contacts at Tide. They have a lab up in Rochester, and I can actually send a dirty game jersey or practice pants, and they’ll develop a formula for me to get that stain out.
I’ve also built great relationships with equipment managers at teams like the Orioles and Commanders. There’s crossover in every sport. For example, we just bought a Sani Sport machine that uses ozone to kill bacteria on a helmet or knee braces in 18 minutes. That was first used in the NHL and now it’s spread.
Winning is the absolute greatest feeling in the world. But you also have to be prepared! At the Duke’s Mayo Bowl last year, Coach Locksley had a nice vest on that day. I got him a different pair of shoes and pullover that were more disposable, because after they poured that mayo on him, we packed everything up and drove eight hours home from North Carolina. We just had to let those things go.
This is part of a monthly series that looks behind the scenes at “what it takes” to keep the University of Maryland humming and create a vibrant campus experience. Got an idea for a future installment? Email kshih@umd.edu.
Maryland Football (1-0) continues its three-game homestand with a matchup against Charlotte (1-0) on Saturday at SECU Stadium. The game is set to kick off at 7:37 p.m. and will be broadcast on NBC and the Maryland Sports Radio Network. Find more details at umterps.com.
Topics
Athletics